Ihr Partner für Lean Consulting und Prozessoptimierung – Effiziente Lösungen für Ihre Produktion.
Von der Analyse bis zur Umsetzung: Wir begleiten Sie auf dem Weg zu optimierten Prozessen und maximaler Wertschöpfung.
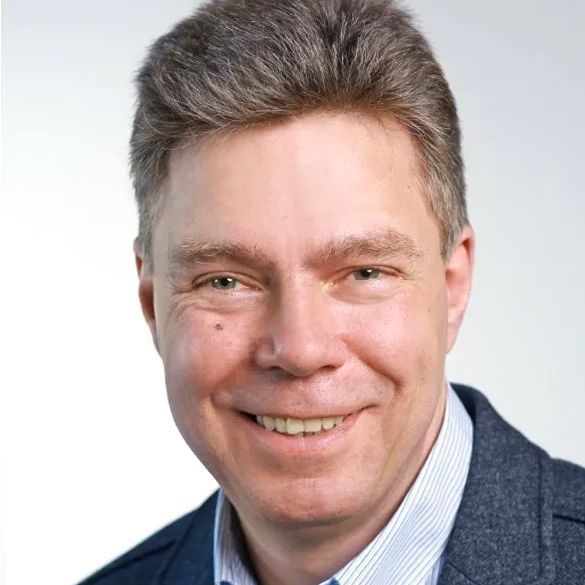
Holger Thieringer
Lean Consultant, Projektmanager, Fabrikplaner
"Lean Management ist der Schlüssel zur langfristigen Wettbewerbsfähigkeit und nachhaltigem Wachstum. Indem wir Ineffizienzen beseitigen und den Fokus auf kontinuierliche Verbesserung legen, schaffen wir echte Wertschöpfung für Ihr Unternehmen und Ihre Kunden.
Kontaktieren Sie mich direkt, um zu erfahren, wie wir gemeinsam Ihre Geschäftsprozesse transformieren können."
Charakteristische Projekte
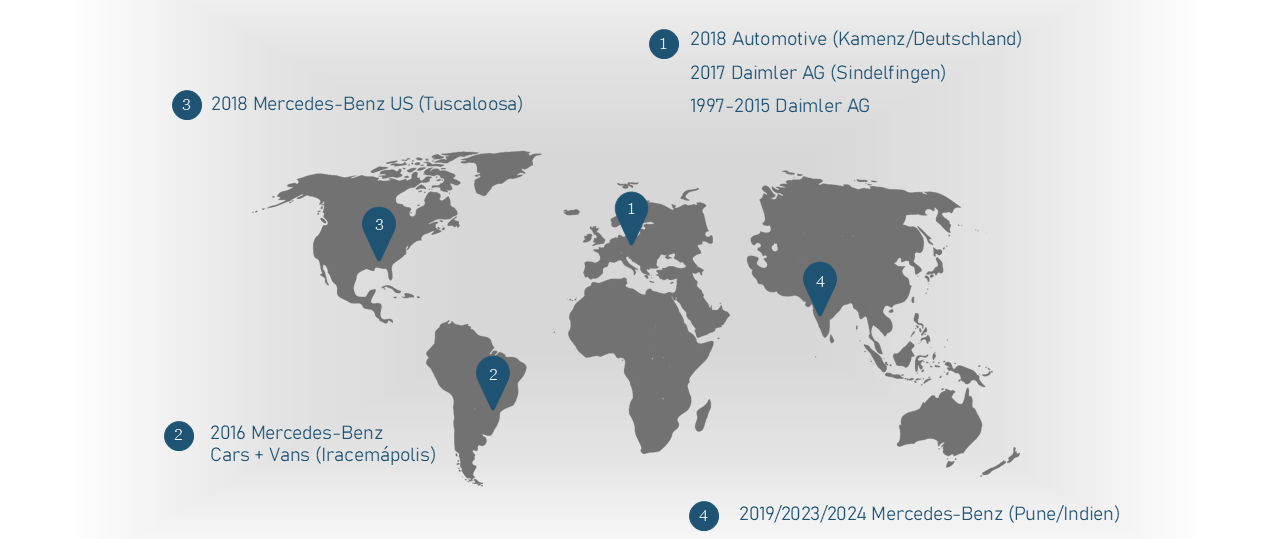
Unsere Lösungen
Mit unserer umfassenden Expertise unterstützen wir Sie dabei, komplexe Herausforderungen in Ihrem Unternehmen zu meistern und nachhaltige Lösungen zu entwickeln, die Ihre Prozesse effizienter, robuster und zukunftsfähiger machen.
Prozessoptimierung
Optimieren Sie Ihre Prozesse – Minimieren Sie Verschwendung und steigern Sie Ihre Produktivität.
Shopfloor Management
Transparenz durch Nutzung von Echtzeit-Daten und zur Entwicklung von Maßnahmen.
Logistikoptimierung
Effiziente Intralogistik für Ihre Produktion – Minimieren Sie Ihre Verschwendung durch intelligente Materialsteuerung und Bereitstellung.
Ursachenanalyse und Problemlösung
Nutzen Sie anerkannte Methoden zur Problemlösung als Grundlage für die Entwicklung von Maßnahmen.
Qualitätsmanagement
Sichern Sie höchste Qualitätsstandards – Optimieren Sie Ihre Qualitätssicherung nachhaltig.
OEE und Rüsten
Optimieren Sie Ihre Rüstprozesse – Steigern Sie die Effizienz und Reduzieren Sie die Ausfallzeiten.
Unverbindliche Erstbewertung – Ihr Schnellcheck zur Effizienz!
- Ob Prozess oder Produktion – wir werfen einen fachkundigen Blick drauf!
Schnell. Kostenlos. Aussagekräftig.
Unsere kostenlose "Musteranalyse" gibt Ihnen messbare Hinweise zur Prozess- oder Qualitätsverbesserung und prüft ob eine Beratung zielführend ist.
Ideal für Produktionsleiter, Qualitätsbeauftragte und Lean-Verantwortliche.
KONTAKT
Impressum
Thieringer Consulting | Holger Thieringer | Pfeifferweg 5 | 72401 Haigerloch | USt-ID: DE 341324199